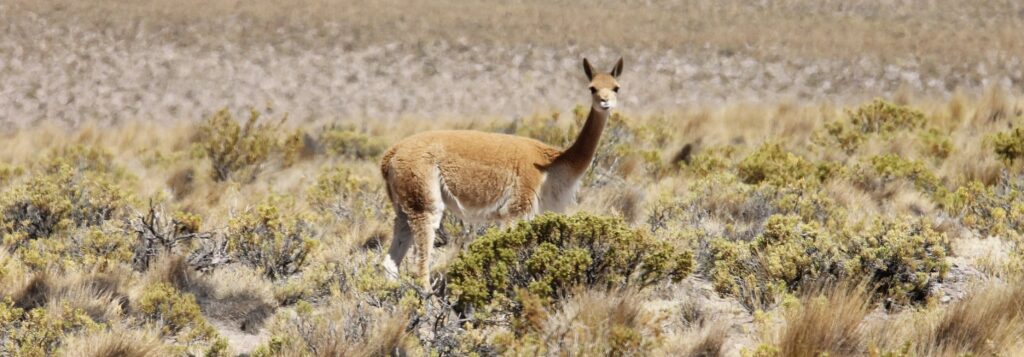
ANIMAL CARE
Livestock is one of the main traditional activities of the Aymara people, and it is precisely from the animals that the fiber that allows Andean textiles is obtained.
Boys and girls learn to take care of animals from a very young age, and in general it is a task carried out to a greater extent by women. They move the herds through different pastures and wetlands, depending on where the food is throughout the year, seeking shelter for cold and windy days; they try to keep predators away so they don't hunt their animals; they are attentive to what happens to the females and that the young do not fall into the water; and in general, attentive to the whole flock as a mother takes care of her children.
SHEARING
The fiber of the alpacas is obtained through the equila. In our region, this is generally done every two years, so that, on the one hand, the length of the fiber is optimal to allow spinning; and on the other hand, that the length that remains in the animal is sufficient to maintain a good body temperature. This is especially important, since the cattle in the tiplano sleep below 0ºC
Traditionally, the shearing is done with tin, which is obtained from oil containers or from pusytunga (a drinkable alcohol of 95º). There are still people who are used to using this means, but little by little the shearing shears have been incorporated and more slowly the electric shearing machine. Whatever the tool to use, for each one you must have a skill such that it allows a quick cut, that does not burn the fiber, that it is even and does not harm the animal. This way you can get the best fleece from each specimen.
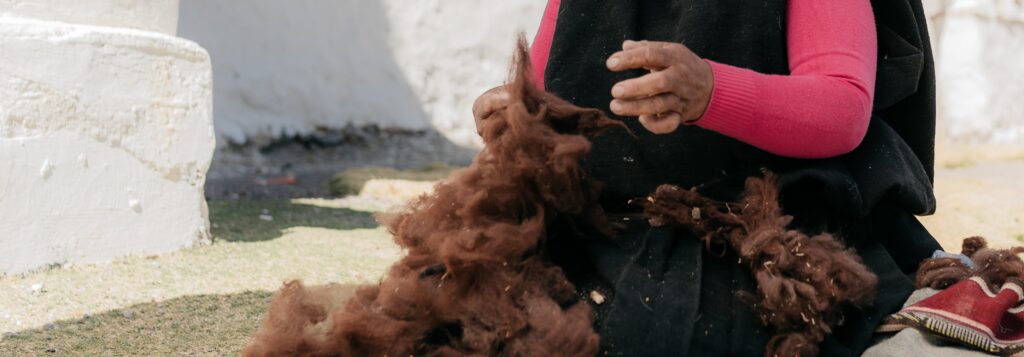
CLEANING AND WEEDING
The fiber obtained in the form of fleece, normally comes dirty and with burnt areas. This is normal since the animals live in natural meadows, passing between mountains and pastures, and taking sand baths to keep mites and other parasites away. Therefore, before proceeding to the next step, the fleece must be cleaned and carded. First, the largest elements that are rooted in the fiber are removed, and also the burned parts that are generally noticeable because they take on another color. Then some artisans pass it through a carding machine, where the fiber is cleaned and untangled, or else they do it by hand as they spin.
YARN
The spinning process is where the magic happens. Through the puska and the expert hands of the artisans, that cloud-like fleece is transformed into a neat, soft and thin thread. The constant turning of the puska plus the definition of how much fiber to deliver, define the thickness that is given to the thread. That thickness will depend on what you want to use it for: if it is for blankets or thick fabrics in 4 stakes, it is spun thick; for light fabrics such as shawls and ruanas, it is spun medium to thin, and for traditional items on the cintira loom, it is spun very fine. The skill of the women artisans means that they can be doing multiple activities while spinning, such as shepherding, talking, taking care of the children, and spinning non-stop.
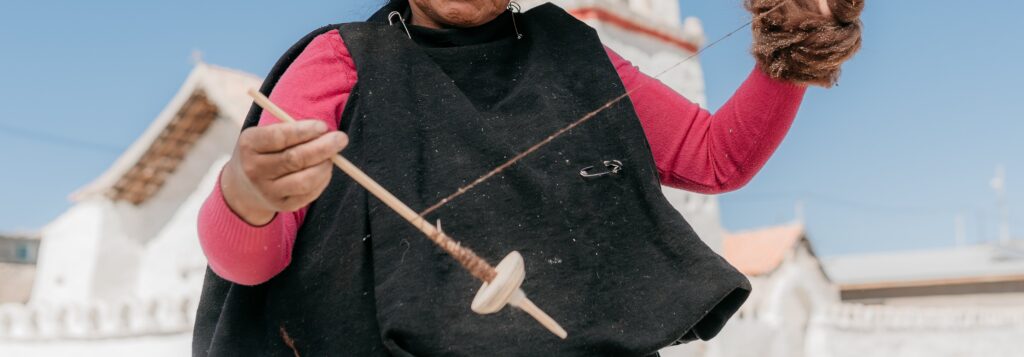
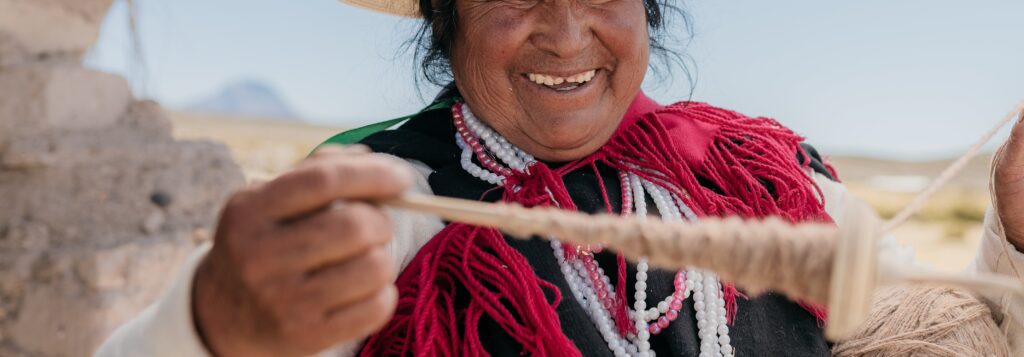
DISTORTED
In a process similar to the previous step, the puska is rotated again, and while it dances, two threads are joined to give the finished appearance to the caito or final yarn to weave. Here the skill guides the level of twisting that is required between both threads, and how to loosen the skeins so that the threads can come out of their core and join each other in a virtuous dance between the hands and the puska
WASHED
The spun and twisted fiber is arranged in skeins. This fiber is still with the fat of the animals, so it must be washed so that the smell of the animals is not so strong on it and its natural softness and colors can shine.
DYED
Alpacas have marvelous colors in their fiber, ranging from white to dark grey, and white to dark brown. However, in order to portray the territory in the fabrics, since past generations the fiber has been dyed, adding green, yellow, red and lilac tones to the palette. Either with natural dyes such as herbs collected in the highlands, or modern dyes, expanding the designs thanks to these colors.
KNITTING
In the fabric, the piece is shaped that between weft and warp, reflects the design that the artisan creates in her mind, and that speaks to us of landscapes, dreams and nature.
With the fiber already prepared with the thickness and color that is needed, the artisan assembles the loom. There are different looms for different shapes, such as the waist loom, where the girdles are made; the one with 4 stakes, in which the awayus are woven; and those made of pine, which can have 2 or 4 pedals, which used to be made of local wood and today are made of iron.
The first thing is to prepare the warp, which is the initial base to be woven and which gives the length of the piece. To crisscross the strands and make the designs, there is the hillagua. In pine looms it is already established, and in the older ones it must be done manually and according to the design to be made.
And then to weave... with patience, skill and focus, weft by weft, crossing and crossing, a piece comes to life, in which each woman tells us with her hands, the stories and desires inherited by so many generations.
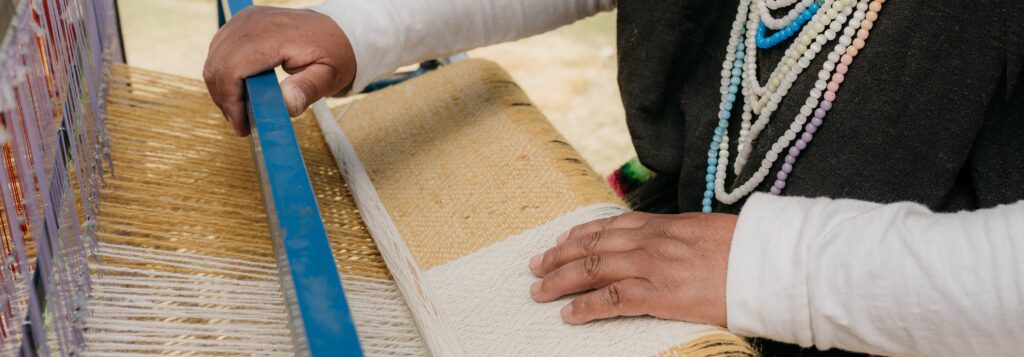
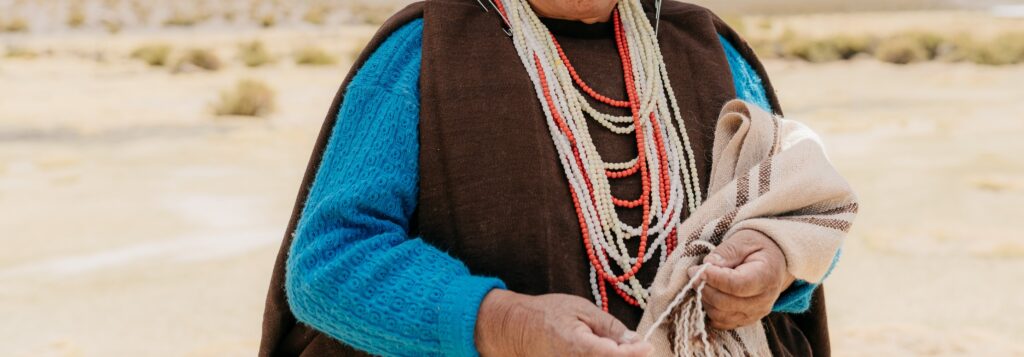
ENDINGS
Finally, to close each masterpiece, the artisan gives the last details. Making edges, fringes, removing lint, joining pieces and ironing, so that whoever inherits this work can sensitively perceive the entire story embodied.